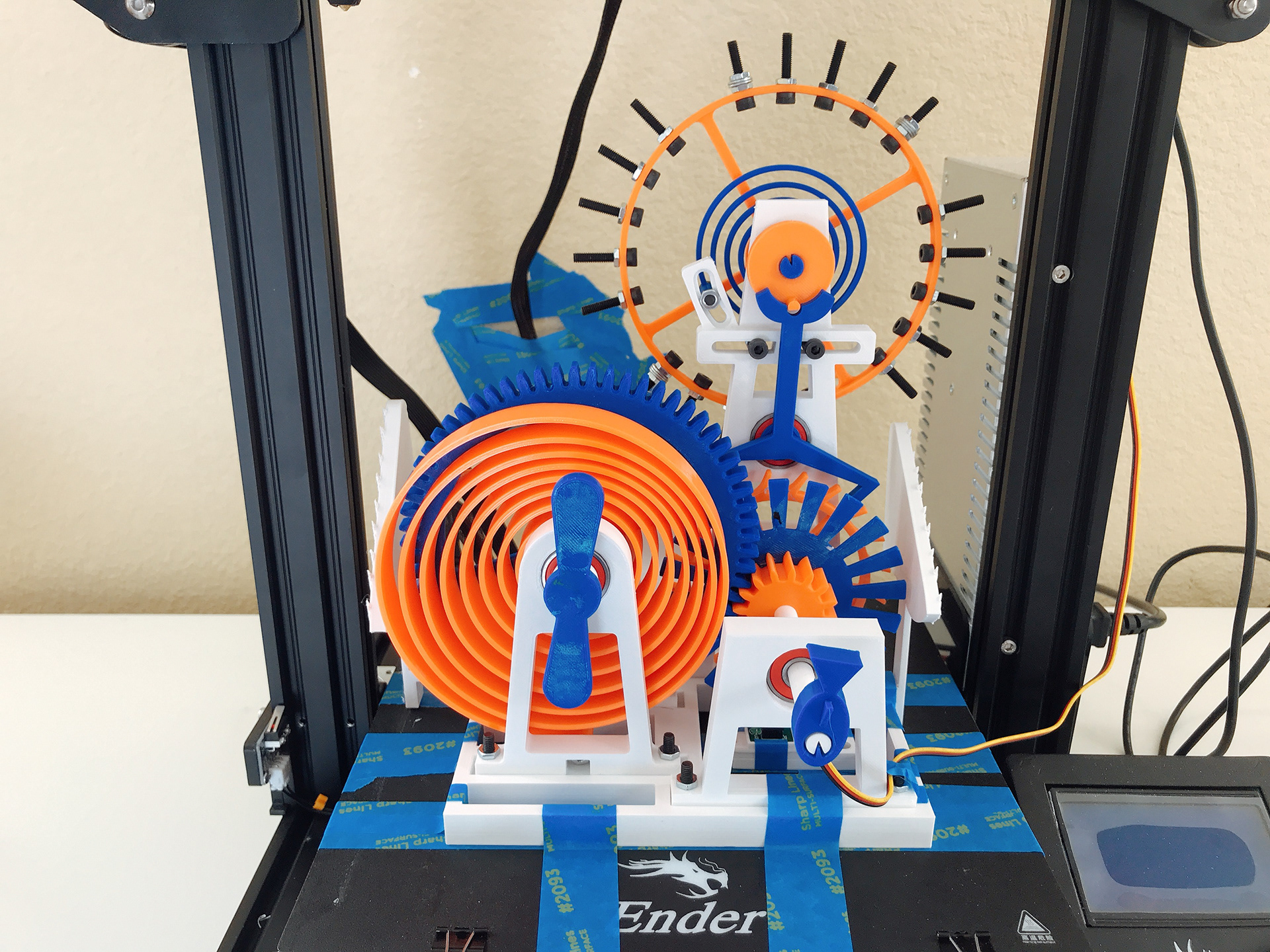
Challenge
Design, test, and build a fully functioning marine chronometer, for use on rough seas and optimized for accuracy and precision.
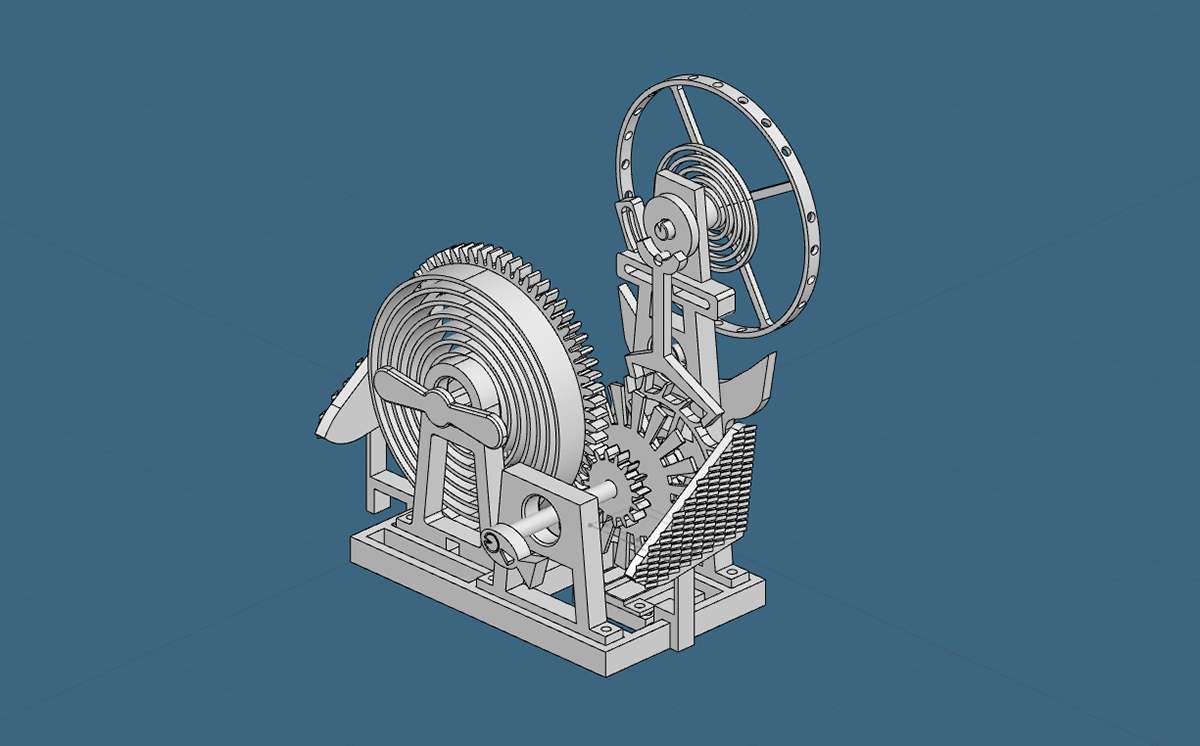
CAD Model
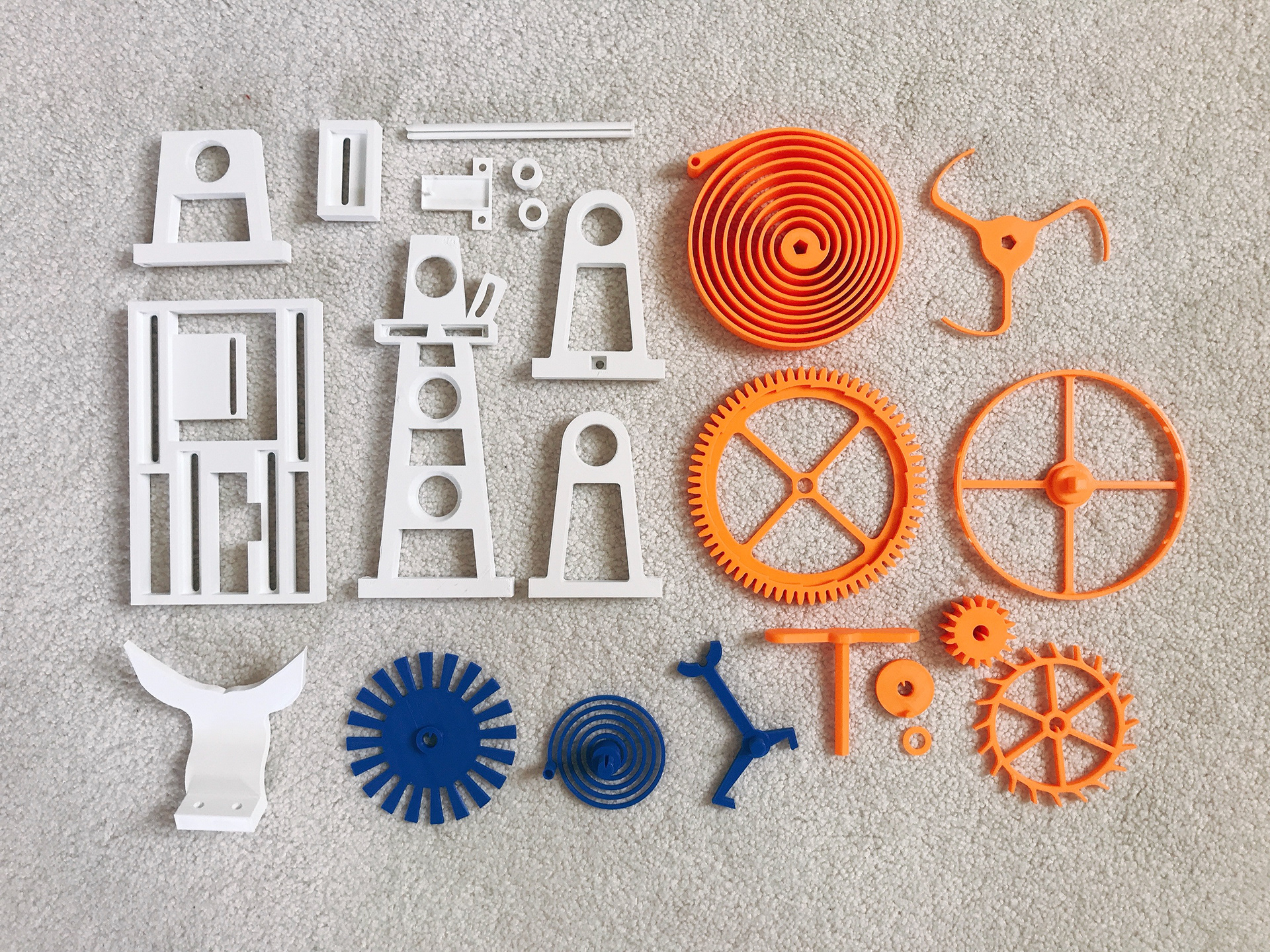
3D Printed Parts
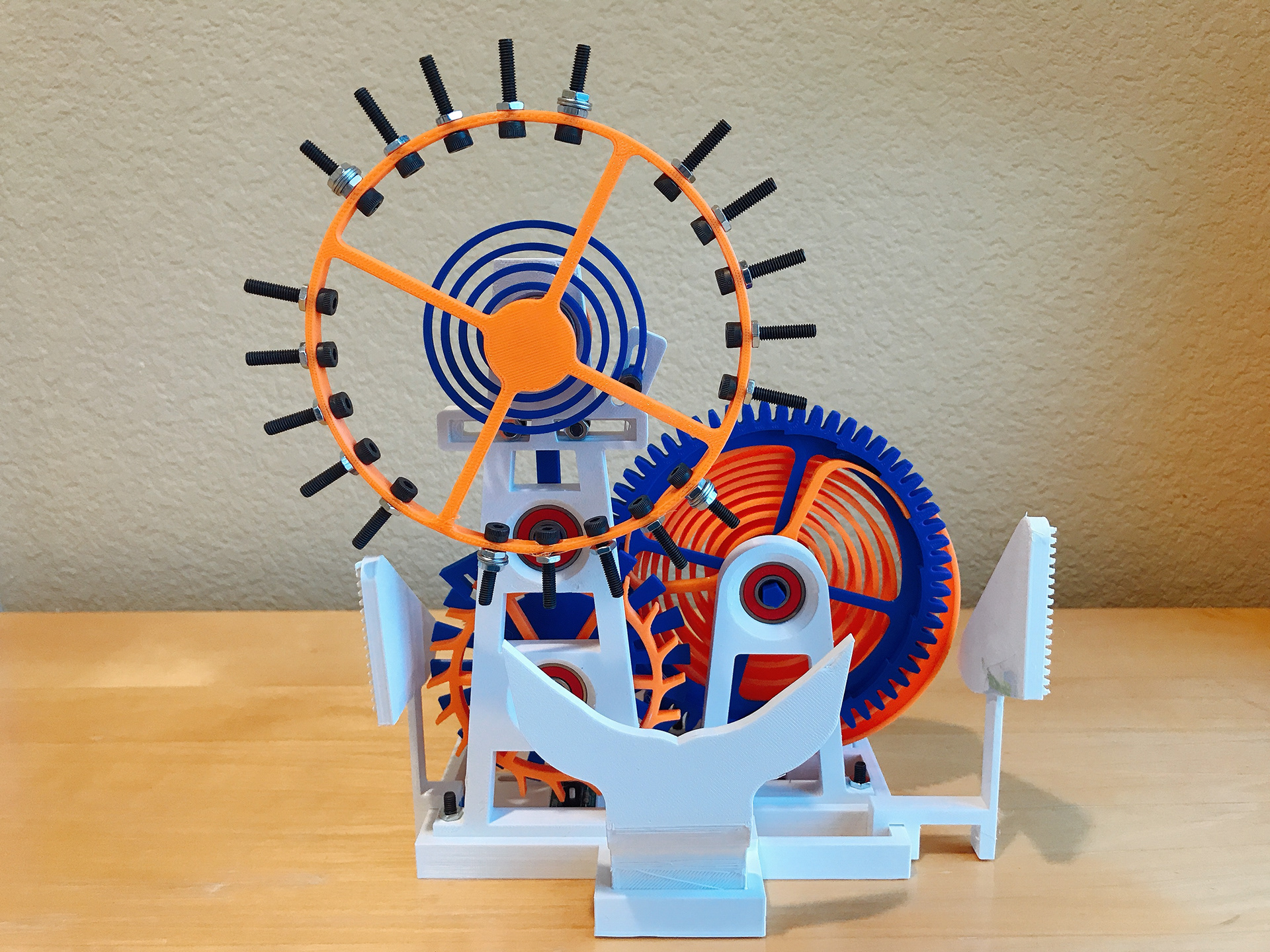
Back View
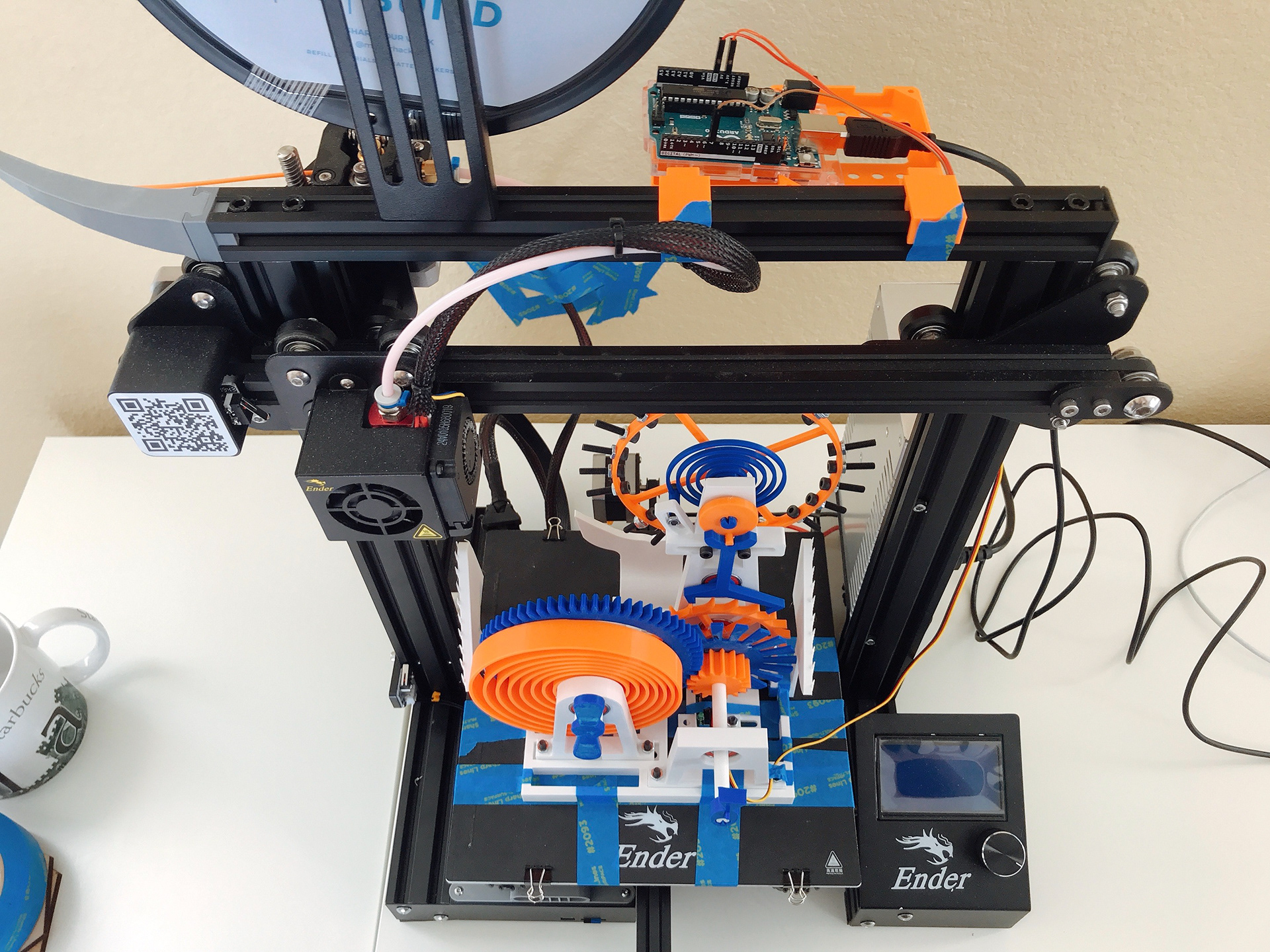
Top View
Project Overview
For my Computer-Aided Mechanical Engineering Design class, we were tasked with creating a marine chronometer that triggered an optical encoder, via an Arduino, at a rate of 60 pulses/minute ± 10% for a minimum of 10 seconds. To simulate the movement of a ship at sea, the clocks were tested while attached to a 3D printer bed, controlled by a G-code program that rocked it back and forth. Our clock went head to head against other teams' clocks in a live competition: data from our clocks were uploaded and analyzed in real time to determine which chronometer was the most accurate, precise, and longest running.
The primary design constraints were time, materials, and dimensions. We had 6 weeks to complete this project and besides a few tools that were provided (i.e. bearings, M4 fasteners), we had to fabricate our clock only using desktop 3D printers. An extra challenge was this all happened during the COVID-19 pandemic. This created additional hurdles because beyond the technical complexity of this mechanical engineering challenge, we also had to navigate how to collaborate, design, and fabricate this assembly as a team 100% virtually.
This project was unique and unexpected in many ways. However, it was an incredible and unforgettable engineering experience!
Design Process & Results
Our clock, as an assembly, went through three major design revisions before arriving at our final design. However, each of the main components (the mainspring, the gear train, the escapement, the balance wheel + hairspring, the housing) went through countless revisions. Each sub-assembly was a complex mechanical component that required skill and creativity to design, and defining the interaction points and meshing these sub-assemblies together into one cohesive, functioning chronometer was even more challenging.
During the live competition, our team's clock performed outstandingly well! Our chronometer lasted for a duration of 4.5 minutes, with 0.2% accuracy error and 99% precision. Compared to the other teams, we had the best performing chronometer - most other clocks could not last beyond 30 seconds and were unable to hit even 50% precision.
Key Takeaways
This project was truly a one-of-a-kind experience, especially given all of the special challenges that COVID-19 and remote learning poses to engineering education, which is inherently hands-on and collaborative. However, this experience was a truly enjoyable and worthwhile experience!
Designing, testing, and building this marine chronometer was a difficult, but rewarding mechanical design project. The mechanical complexity of a clock, requiring such tight tolerances in the sub-assemblies themselves as well as in their various interaction points, along with having such heavy design constraints made this project particularly challenging. Furthermore, beyond pure mechanical functionality, optimizing the accuracy and precision of a clock requires an equal amount of energy and creativity, which forced us to overhaul many initial design ideas, constantly iterating designs in order to fine-tune our clock.
Because of this project, I learned more advanced mechanical design techniques, such as drawing involute gear tooth profiles and drawing springs of different spring constants in CAD software. I had to apply a wide range of engineering theory, including energy principles (storage, transfer, efficiency, friction), gear knowledge (meshing, compound gears, gear trains), and geometrics (dimensions, tolerances). Also, given the remote nature of this inherently hands-on and collaborative engineering experience, this was a unique and eye-opening team experience. I learned a lot about virtual collaboration, clear and transparent communication, and project management.
Overall, this virtual learning challenge was an incredible experience, and I feel more readily equipped and confident as a mechanical engineer and teammate.
Skills & Documentation
Skills: xDesign, xShape, Simulation Tools (CAD) | CAE/CAM | DFM | GD&T | 3D Printing | PrusaSlicer | Project Management
Documentation: Project Description, Written Report, ENGS 146 Class Portfolio, "Dartmouth Engineering Students Step Up to 3D Clock Challenge"
A special thanks to my teammates: Lylia Eng, Ledane Ram, Rafa Rosas, & Mikey Steel
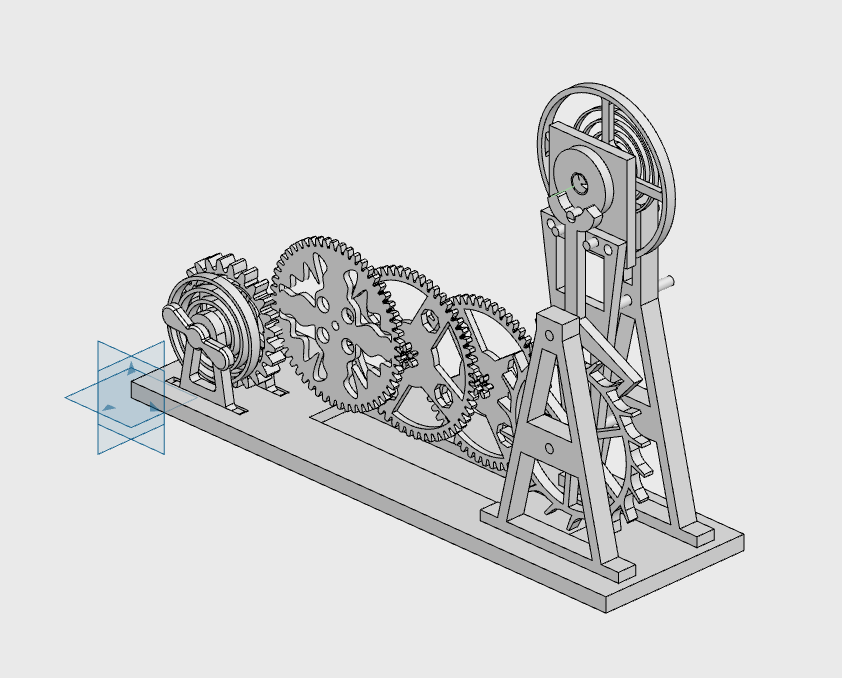
Revision A: CAD
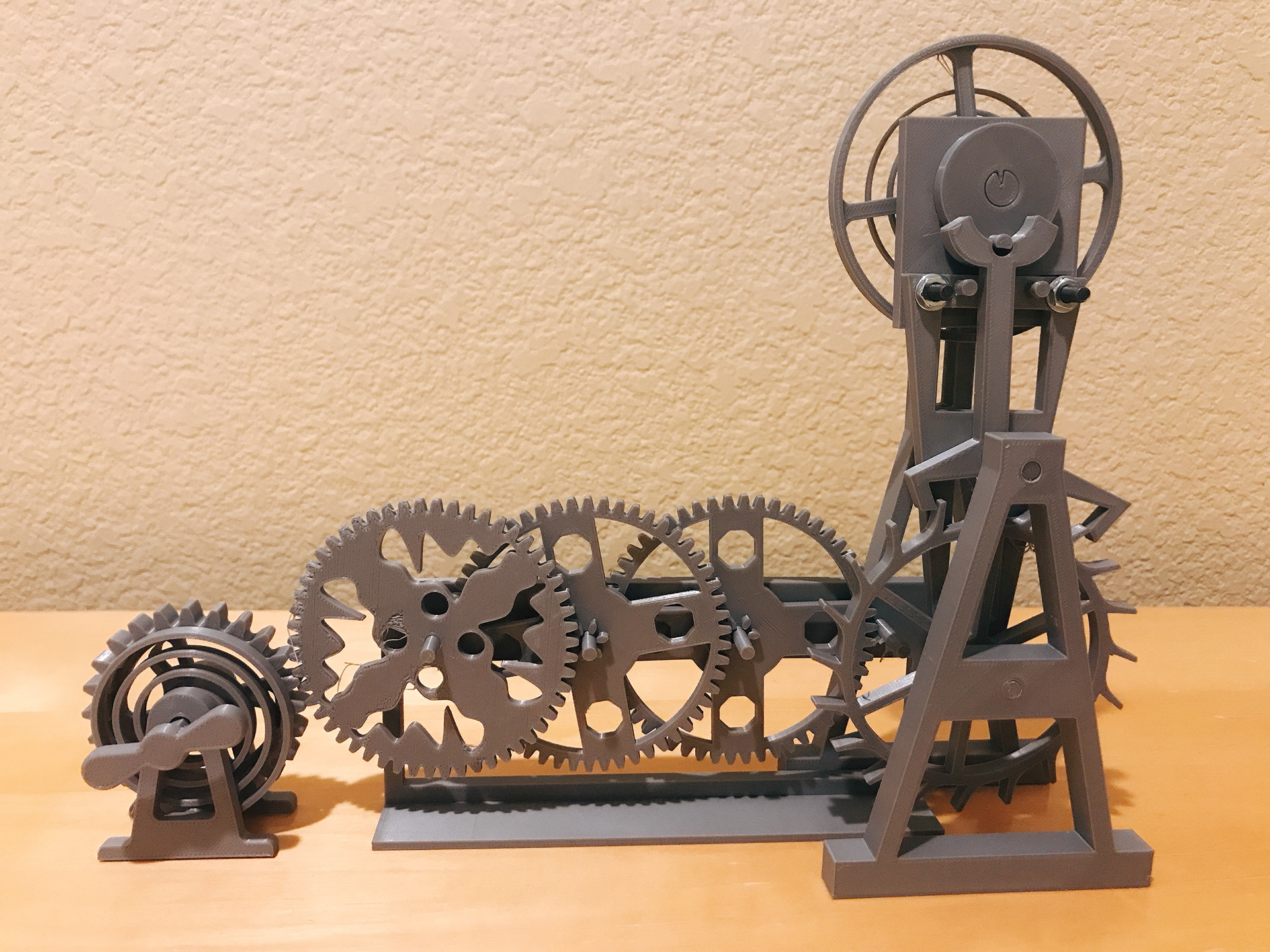
Revision A: Print
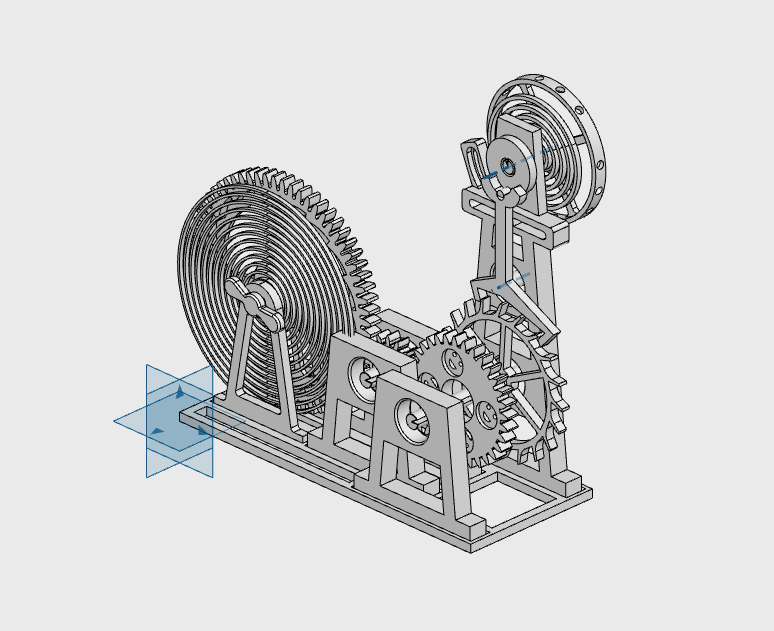
Revision B: CAD
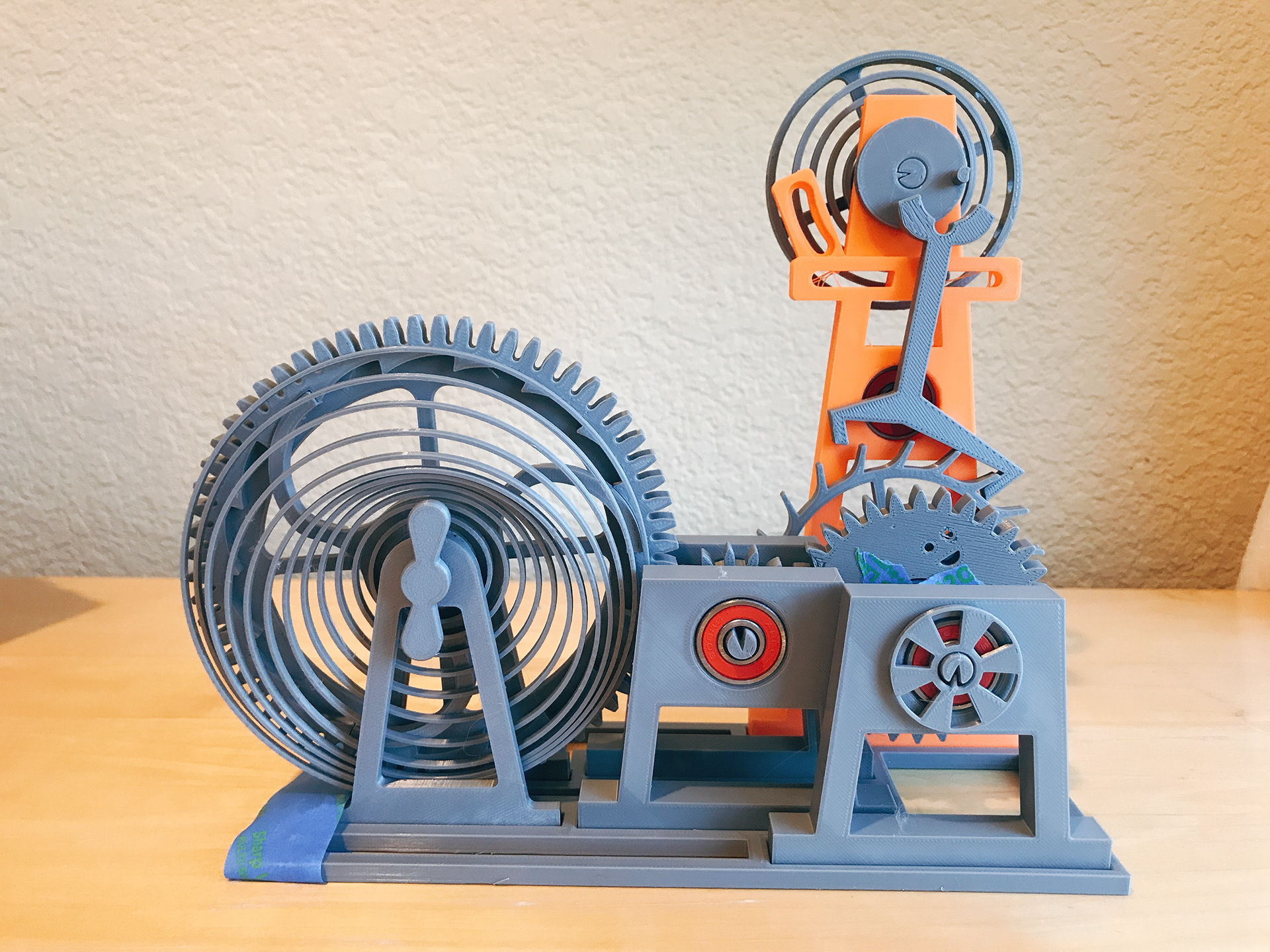
Revision B: Print
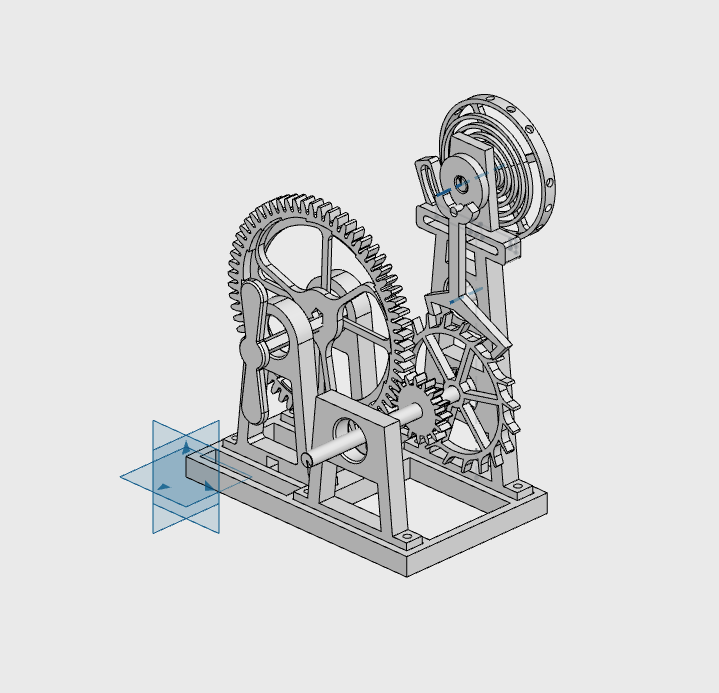
Revision C: CAD
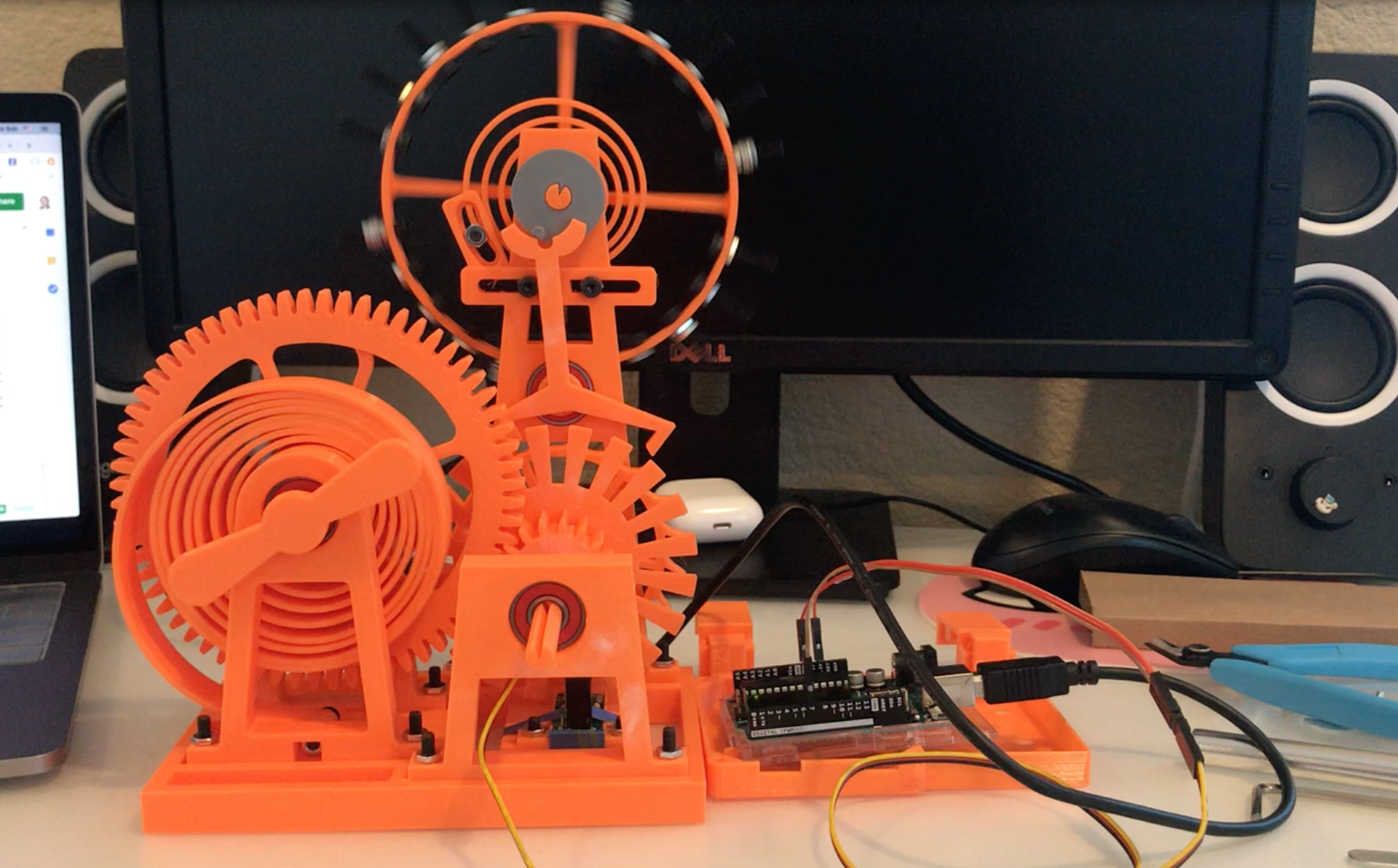